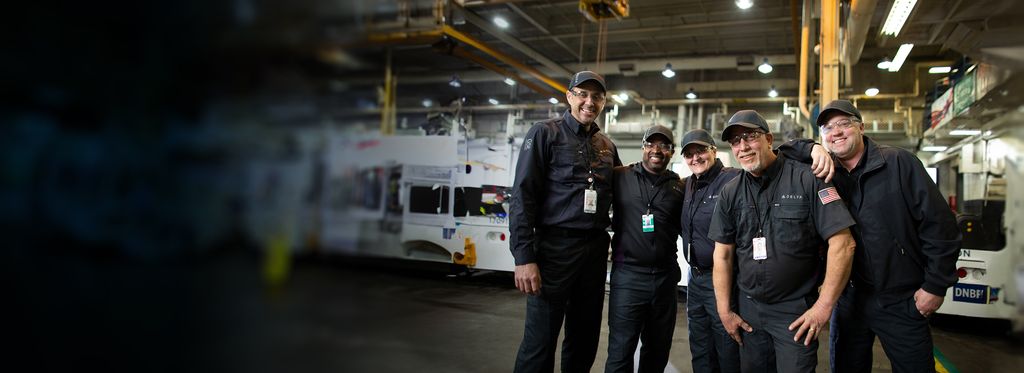
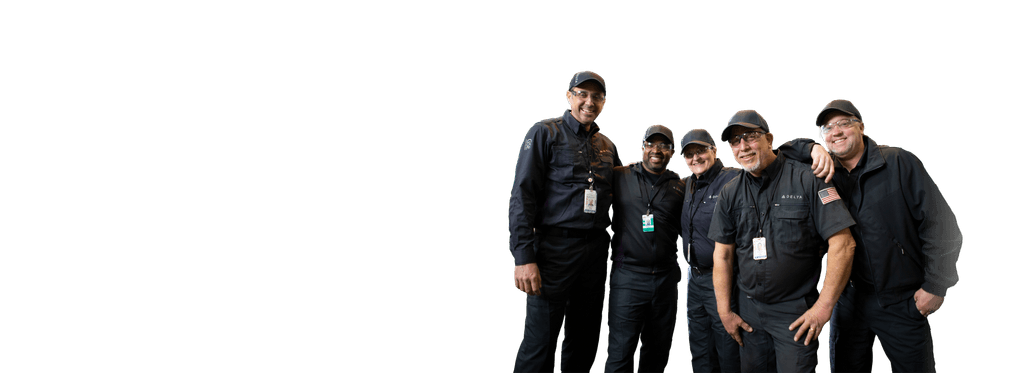
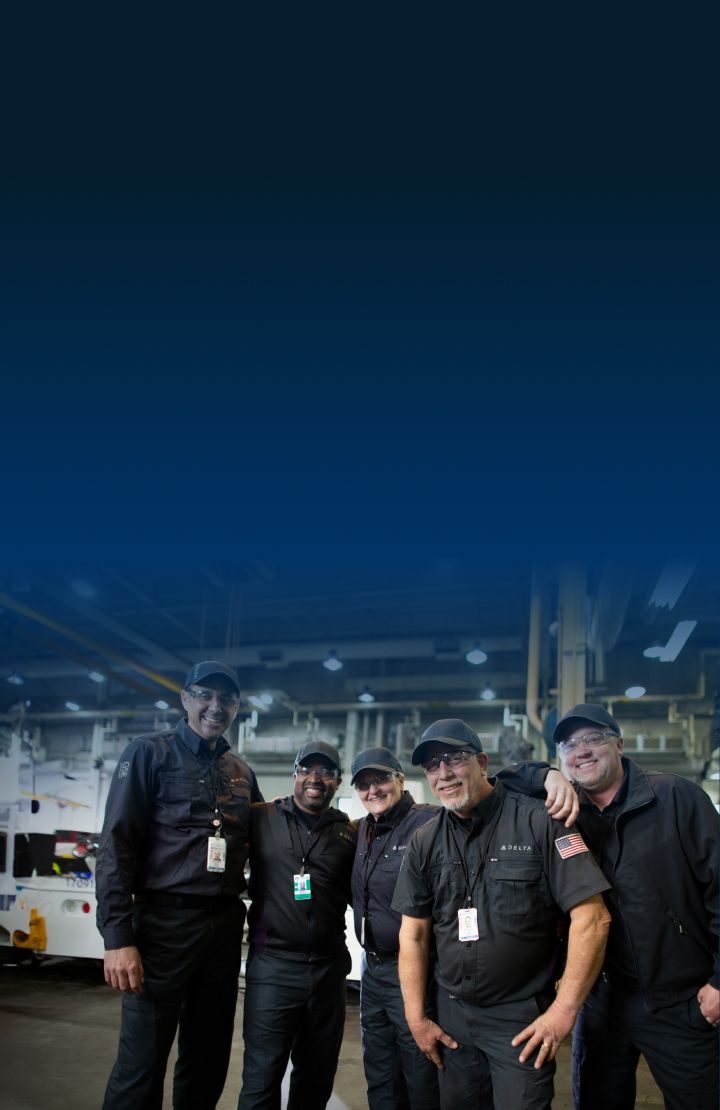
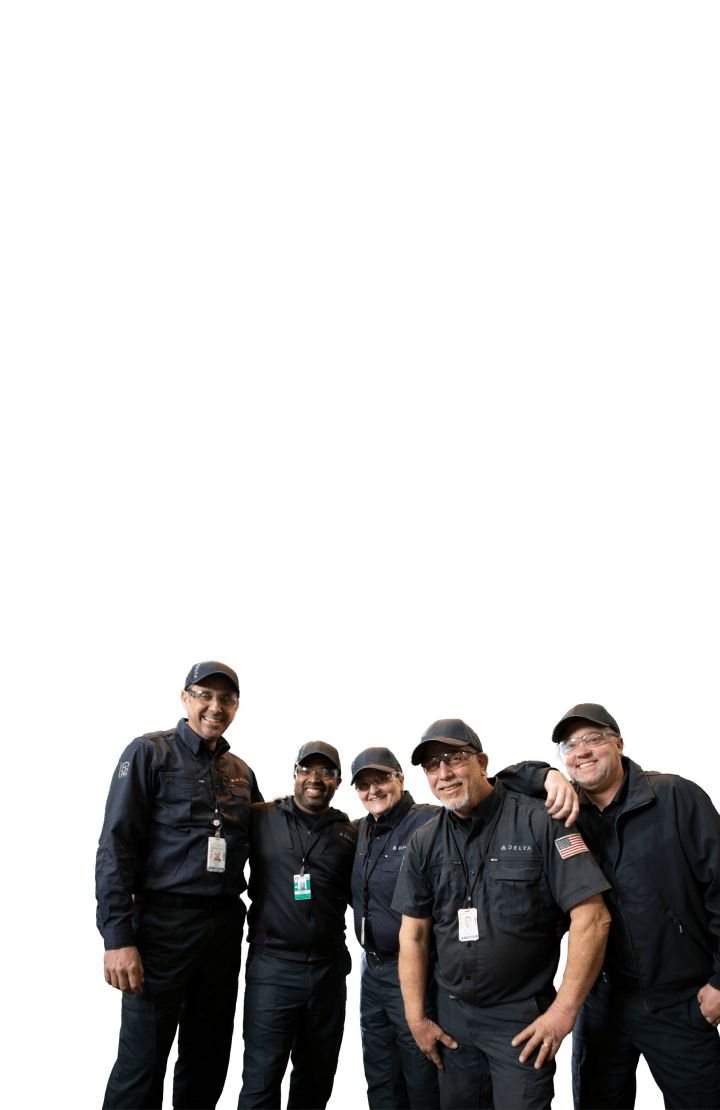
Safety Management System
Delta’s SMS is our holistic approach to ensuring both occupational and operational safety throughout the company. Delta’s SMS also applies to operations performed by Delta’s business partners and contractors who support the Delta operating divisions. Through safety management protocols, the SMS prioritizes hazard identification, risk assessment and mitigation, safety performance monitoring and the promotion of a company-wide safety culture.
In 2017, Delta was one of the first U.S. airlines to receive validation from the Federal Aviation Administration (FAA) upon implementation of our SMS and we continue to elevate our approach to safety management. Delta is a signatory of the International Air Transport Association (IATA) Safety Leadership Charteropens in a new window, which is designed to demonstrate commitment to cultivating a positive safety culture.
Safety Leadership is an essential element of our SMS, and key to our success. Safety Leadership comprises a set of behaviors demonstrated by individual actions that drive our overall safety culture and are promoted company-wide. These include integrity, clear communication, accountability, listening and care. Through each and every employee embracing these characteristics, we continue to illustrate our commitment to the safety of our people and customers and to making safety our number one value.
Began using artificial intelligence to analyze operational safety reports and started investing in upgrades to reduce and address instances of hot cabins.
Delta's Safety Leadership Circle showing "Safety Culture" at the center, surrounded by "Policy," "Risk Management," "Assurance," and "Promotion".
Safety Culture
Delta’s Code of Ethics and Business Conduct — titled The Way We Fly — reinforces our safety expectations and standards for employees and business partners around the world. We are committed to embodying the principles of Just Culture, in which employees and partners are empowered to report hazards and mistakes, leaders are accountable for responding in a fair manner, and we are all committed to continuous improvement and prioritizing learning from incidents.
Our Safety Reporting Programs are a cornerstone of Delta’s safety culture and SMS. These programs ensure all employees have an easy and effective way to share safety concerns and inadvertent deviations from policies and procedures. We maintain voluntary hazard reporting programs for all frontline employees that encourage the confidential disclosure of any potential incidents that may affect our overall safety performance. In 2024, nearly 89,000 front line employees including pilots, flight attendants, dispatchers, load planners, schedulers, ground agents, maintenance personnel and engineers had direct access to voluntary hazard reporting. Delta is committed to a culture where employees may freely share safety concerns and inadvertent deviation from policies and procedures without fear of retaliation.
We understand that people sometimes make mistakes while trying to do the right thing. Just Culture focuses on implementing lessons learned rather than placing blame on individuals. In 2024, Delta employees reported 127,260 safety concerns internally, helping us to continue proactively managing risk.
Addressing Risks Related to High Temperatures
Delta’s work environments at airport facilities and in aircraft cabins are subject to high temperatures seasonally at some of the airports we serve, particularly in the south and southwestern parts of the U.S.
SMS provides the framework to proactively manage risks related to high temperatures. We use data from Occupational Safety and Health Administration (OSHA) recordable injuries reporting, employee safety reports, equipment reliability reports and customer experience reports to provide an understanding of our risk profile related to heat-related issues. These risks are continually analyzed and discussed on a weekly, monthly and quarterly basis by our safety and operations teams – and ultimately reviewed by our SMS Accountable Executive(s) with the Safety and Security Committee of our Board of Directors. In addition, heat-related risks occurring at airport locations where Delta utilizes third-party contractors is reviewed monthly and quarterly to ensure safety risks are regularly discussed and addressed with those providers. In 2024, Delta had five recordable heat-related injuries or illnesses.
Airport Ramp Environment
We maintain Heat Injury/Illness Prevention Plans locally to minimize heat risk in our ground operations (or ramp) environment. These plans are maintained by Delta and our contractors. While the plans are developed and maintained locally, all plans must include the following elements:
- Access to water
- Access to shade
- Emergency procedures
- Training on the plan for all employees
Additional procedures may include safety alerts, leadership check-ins with employees and working with a buddy to watch over each other during periods of high temperatures. The plans are updated annually by local and corporate leaders and checked by safety compliance auditors no less than once every 24 months. While we make our best effort to execute a strong, comprehensive plan, we also recognize that the policies and procedures may not cover all situations in our dynamic environment. Therefore, our culture is one of empowerment, where any employee or contractor may call a “Safety Time Out” to pause to correct a safety issue, including heat-related issues, and they will be fully supported by senior leaders. Furthermore, we are proud to be in our third year of partnership with the Korey Stringer Institute, guiding Delta in our efforts to proactively address the risk of heat-related injuries/illnesses, which includes evaluation of uniforms, new training and town halls across the Delta system.
Aircraft Cabins
High temperatures, maintenance challenges or other factors sometimes lead to elevated temperatures in airplane cabins, especially during ground operations. In extreme cases, passengers, flight and cabin crew, and ground team members servicing aircraft can experience conditions that present personal safety and health risks. We are upgrading air conditioning units across the system, and we have developed proactive weather alerting that identifies airports and flights with increased risk of a hot-cabin incident. These alerts allow for timely preparation — not only of our equipment to support customers on board, but also for our employees and our contractors who are exposed to the effects of higher outside air temperatures, to have the necessary means to avoid or manage hot-cabin events. For example, in 2024, Delta invested $4 million in air conditioning units at stations with the highest risk of hot cabins. Looking forward, we plan to continue investing to lower the overall age of equipment.
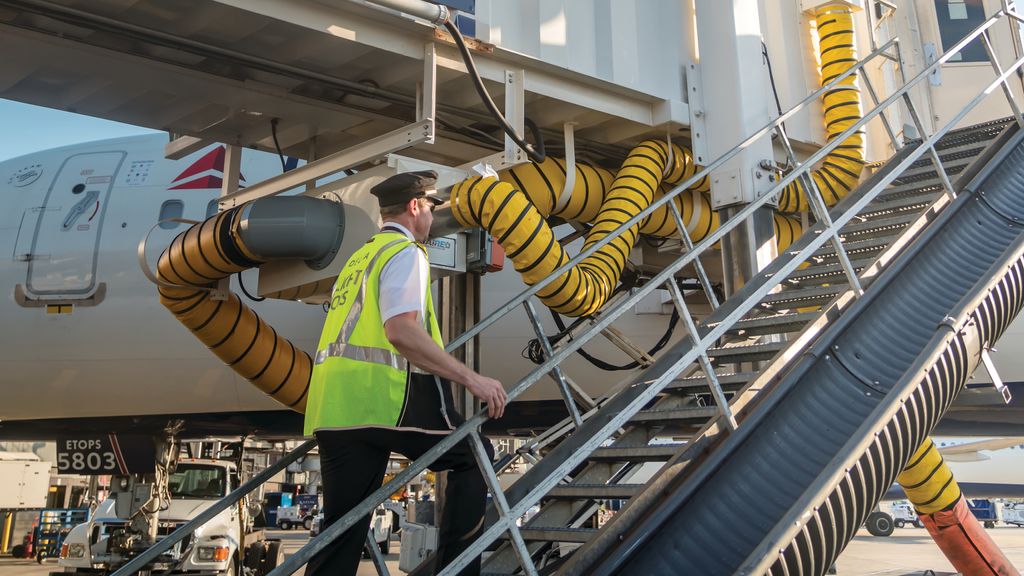
Proactive Safety Management
As part of our SMS, Delta uses Safety Risk Management (SRM), a process through which we proactively identify potential operational hazards and put into place controls to mitigate risk. At Delta, we consider SRM an essential element of change management and it is routinely applied as changes occur around the airline, including:
- Implementation of new systems, such as a new aircraft type
- Revision of existing systems, such as procedural or manual changes
- Development of new procedures, such as adding new airports to our network
- Identification of new hazards or ineffective risk controls through proactive analysis of our safety data
Delta continues to explore and leverage new technology to enhance safety management. For example, in 2024, Delta safety teams began testing the use of artificial intelligence (AI) to analyze operational safety reports. The AI tool’s speed and accuracy reduce the amount of time our experts spend on administrative tasks, allowing more time to consider both the trending risks in our complex air travel industry and the mitigations needed to address those risks. Importantly, even with this application of AI, a human is always present in the safety system to assure the quality of reporting and analysis. Moving forward, the safety teams will train and evolve the AI capability to assist with how we analyze risk within and across operational divisions.
Flight Safety Technology
As part of our commitment to proactive safety management, we are sharing and communicating performance data with pilots as it relates to safety so they can make adjustments in real time. This includes continuing to expand the use of FlightPulse, a strategic impact app that transforms raw flight data into clear, actionable insights. FlightPulse enables pilots to analyze data associated with their flight plans to assess how they compare against standard operating practices, as well as other peers. FlightPulse can also be used in flight to observe any relevant top risks at any given location — including weather, historical trend data and regulatory considerations — and make necessary adjustments midflight. With a pilot interest rate of 95% across fleets, Delta pilots are using FlightPulse, a key tool for ensuring safe operations.
Aircraft Deicing
We also continue to enhance management of the key seasonal risk area of aircraft deicing. Prior to the upcoming season, we proactively review lessons learned from the previous season, update procedures and reinforce key concepts through training, including modern virtual reality training. Furthermore, we leverage robust assurance through employee reporting, routine audits during storms and continual proficiency checks of our deicing teams throughout the season. The data from these sources allows us to take a risk-based approach when analyzing performance and addressing issues. All of these items assure we proactively manage risk to ensure safe operations.
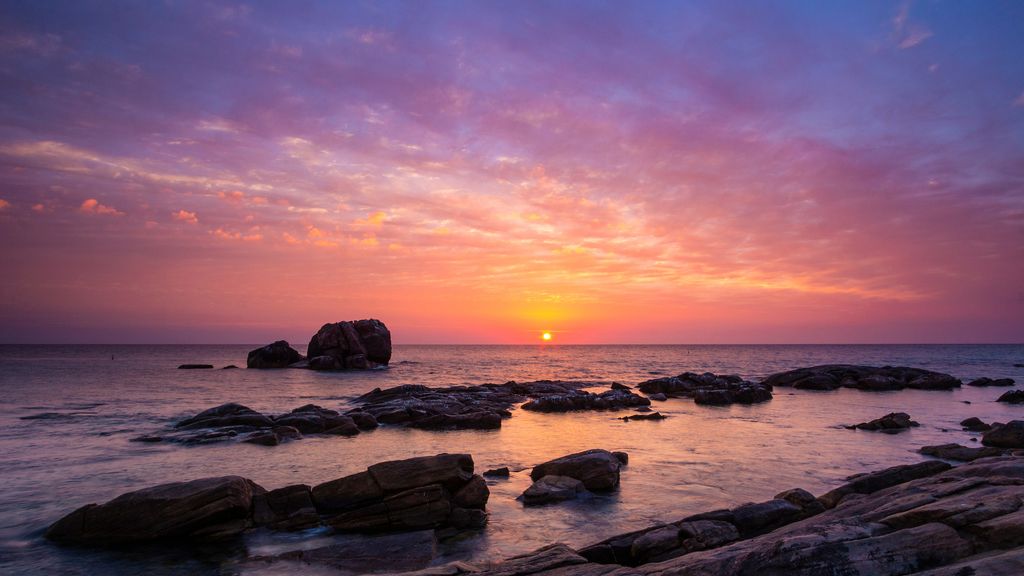
At Delta, we are committed to running the safest operation possible. Our people and our business partners are empowered to take all necessary steps to ensure the safety of themselves and those around them. This includes stopping or slowing down operations if there are safety concerns that need to be addressed. Our people are Delta’s most important asset, and we work to ensure their utmost safety at all times. However, despite our thorough safety preventative measures, accidents may still happen.
In August 2024, a tragic accident occurred in our wheel and brake shop at our Atlanta TechOps facility and we suffered the loss of two beloved Delta family members; a third employee also suffered a serious leg injury. The accident occurred while disassembling a wheel and tire assembly.
Immediately following the accident, Delta took steps to make available a special contingent of health care professionals as part of our Employee Assistance Program, to ensure the mental health and well-being of anyone affected.
Delta Corporate Safety led an internal investigation that resulted in existing safety protocols being reinforced and additional procedural measures being put in place to further ensure tire deflation prior to disassembly. Delta also fully cooperated with the investigations carried out by the FAA and OSHA.